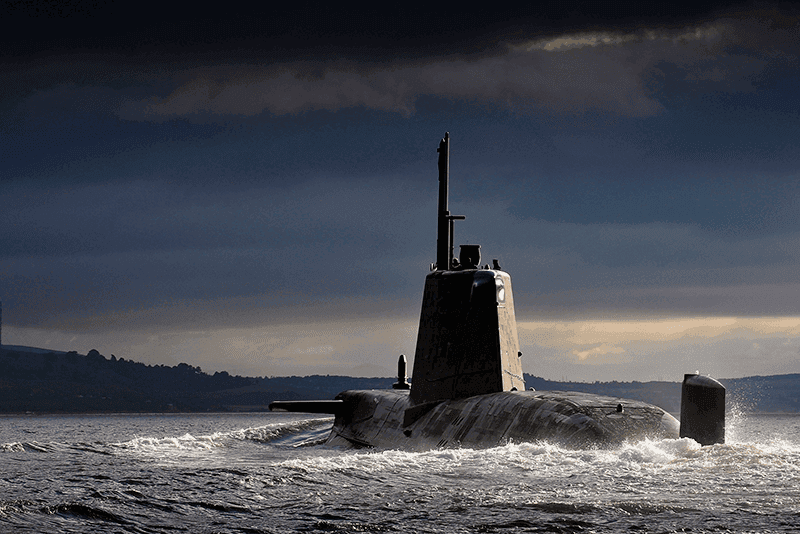
BLOG
How IMI is pioneering new testing and validation for Defence customers across the world
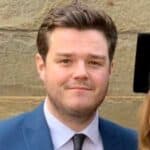
Written By Tom Morton
September 20, 2024
In almost all cases, industry standards are sufficient to guarantee a consistent level of performance. This consistency is key because it signals what customers can expect and what confers confidence.
But in naval marine environments, there’s a need to stretch the limits of accepted standards. Some might question why this is necessary. Experts develop industry standards according to a rigorous set of scenarios and requirements. So why go further?
For IMI, this fails to acknowledge a basic premise for defence work: innovations are only innovative for so long, and because the stakes are so high, there’s a need to push the limits of every design. In doing so, navies can maintain a competitive edge for longer periods. This edge ultimately protects servicepeople – and the general public – from today’s diversifying threats.
The development of IMI’s Acoustic Control Vantage is one of the best examples of our approach. Using ACV as an example, this blog examines the extensive testing and validation procedures that all IMI Truflo products undergo, allowing us to reimagine complex engineering challenges for customers working in the most critical environment on earth.
Going beyond
Like any business, IMI still has to comply with industry norms even if we see value in going beyond the minimum testing requirements. It’s not so much ripping up the rulebook as using standards – such as MIL-STD-1474 and MIL-STD – as the starting point.
The US military issued these two standards concerning airborne and structural noise. For valves, they state designs should be tested fully open at 100%, 50%, and 5% flow rates.
This is important because it cuts to the heart of our initial problem statement when developing ACV. We believed that valves were too loud for defence environments, especially those fitted on submarines. However, most customers initially disagreed, as their designs had passed the tests.
This assessment is flawed because the standards only specify testing in a steady and controlled state. This narrow scope makes several assumptions about how today’s valves operate and what noise levels can be achieved.
For IMI, a more accurate judgement of a valve’s performance can be made when tested according to in-service conditions – i.e. replicating a fitted and operational environment. This strongly indicates a design’s true capabilities as the test resembles real-life conditions.
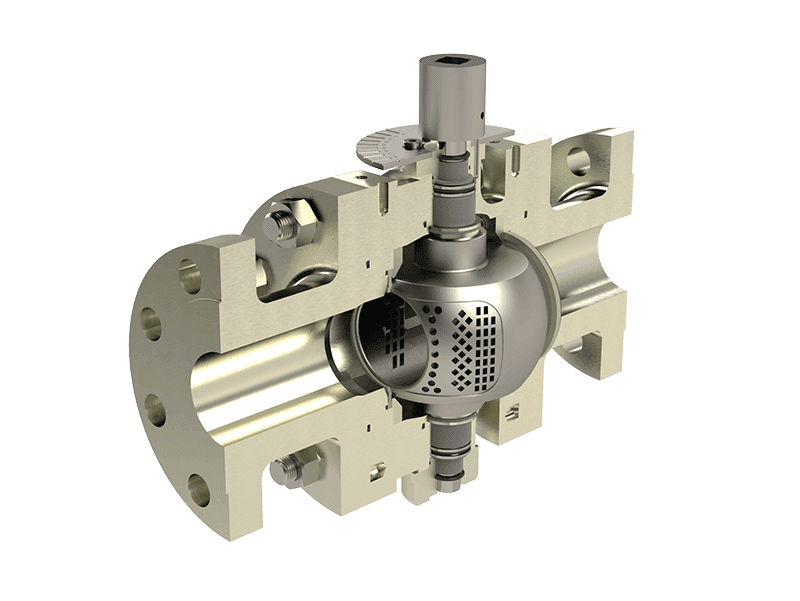
ACV’s tortuous flow path geometry is critical to reducing noise
Reaching the Source
Outdated standards make it difficult to determine the efficacy of innovations like ACV because the product is assessed to a limited specification.
This situation has led the team at IMI to develop more advanced testing and simulation procedures, bringing together data on airborne, structural and fluid-borne noise. The latter is particularly important as fluid pressure changes within pipework are the source of noise generated within a fluid system, and the airborne and structural noises measured by the standards are secondary effects when a vessel is working at sea.
The most significant improvement is the measurement of the transient noise that is generated during a flow control operation of the valve. This is when the greatest noise is generated, and there is, therefore, the highest risk of the submarine being detected as a result of this operation in service. The MIL standards do not specify this type of testing to be completed for valves; instead, testing is required only when the valve is in set positions. IMI has introduced a range of different speeds and flow rates, such as those found when a valve is being used on board a submarine.
We create these conditions using sophisticated computational fluid dynamics (CFD) and vibroacoustic simulations. Using these modelling tools, we can explore how fluid behaves in a pipe system and how it affects the structures surrounding it. This finite element analysis (FEA) is critical because it allows us to predict the noise generated in a given scenario more accurately and test valve performance under operating conditions of pressure and flow that are impractical to replicate during physical testing.
It’s not difficult to see the value of this information, particularly when a vessel is caught in high-alert situations. Yet fluid-borne noise is not currently listed within current standards, and it’s only through our work with institutions like the University of Adelaide that this area of research is beginning to take hold within the defence world.
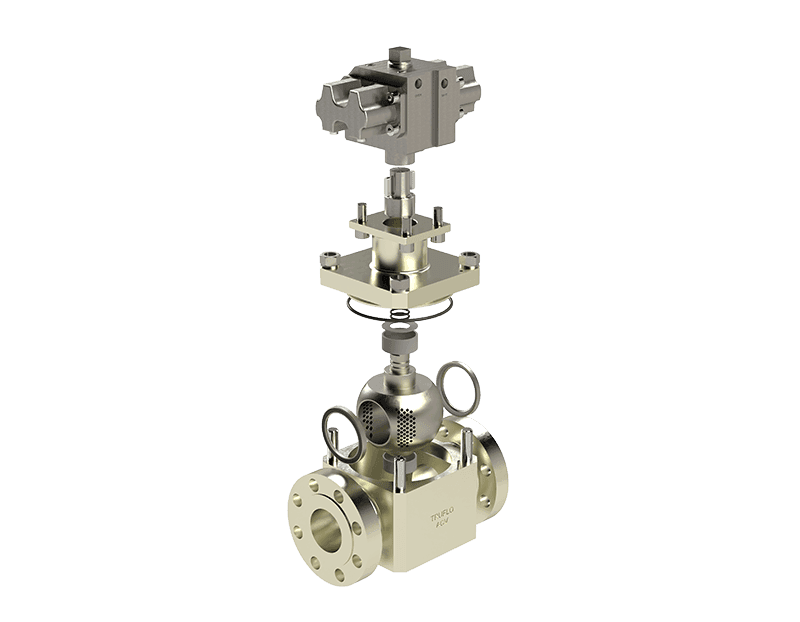
Exploded view of the ACV valve
Shock Validation
Laser powder bed sintering is the optimum manufacturing method for producing the tortuous flow path geometry critical to the performance of ACV technology. Additive products have metallurgy different from conventional materials made in a foundry, making them an unknown quantity, particularly for resisting corrosion when exposed to seawater environments for prolonged periods of submarine service.
ACV also uses unconventional structures. These structures are fundamental to the valve’s performance but also create a risk in terms of unwanted marine growth. This is a common challenge in naval marine environments and, when left unchecked, can cause significant downtime and avoidable maintenance costs.
In order to proactively quantify this risk and establish mitigating solutions to these potential issues, IMI has funded specialised testing procedures far beyond the scope of conventional defence and industrial laboratory corrosion tests. This work, which takes place in real marine environments, has demonstrated the technology’s ability to resist degradation, paving the way for wider use of additively manufactured parts within valve designs.
The use of additive parts must also be tested for shock resistance. Hull valves create the boundary between the open sea and the submarine interior, where crew live and work. As such, it’s critical to demonstrate resistance to the types of underwater explosions created by enemy weaponry.
Again, IMI has employed FEA to test and optimise designs virtually without incurring the expense and time required to manufacture multiple prototypes for physical testing. This also allows us to understand component and material behaviour at a far more detailed level than can be achieved with conventional calculation methods alone.
These are just some of the methods that demonstrate IMI’s extensive testing and validation capabilities. Investment is now being provided for a bespoke facility at IMI’s Aston site, which will further refine and expand our research without the need to use third parties.
Keep in touch
Stay up to date on all the latest news and articles from IMI.
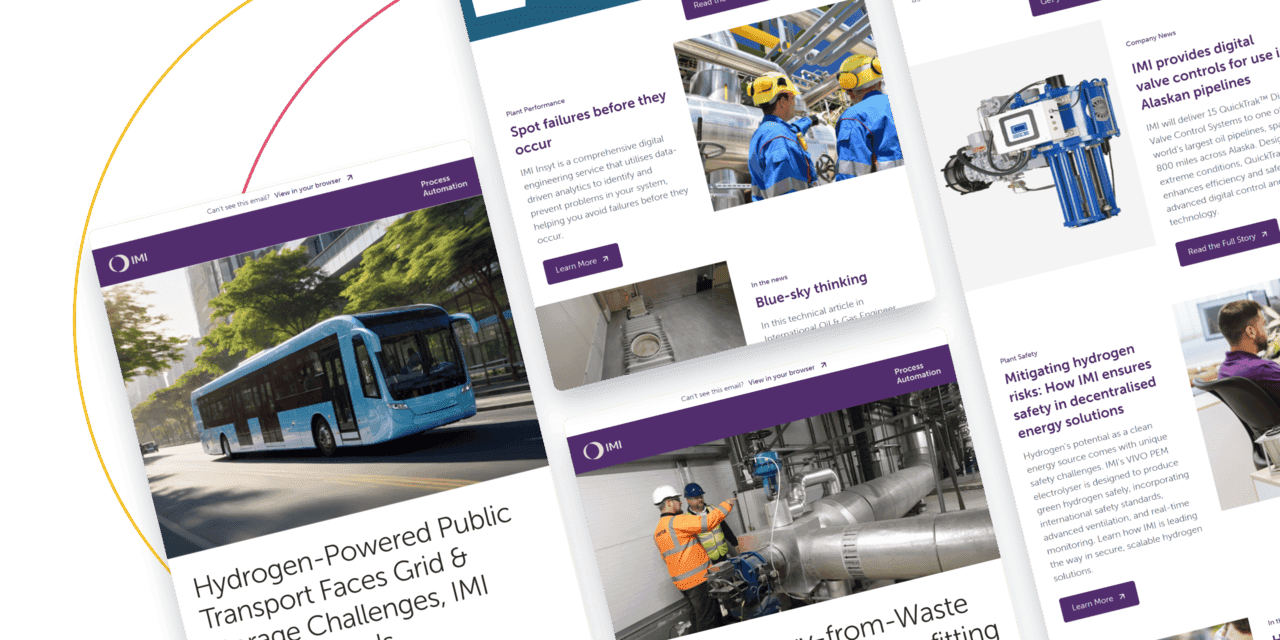
Keep in touch
Stay up to date on all the latest news and articles from IMI.
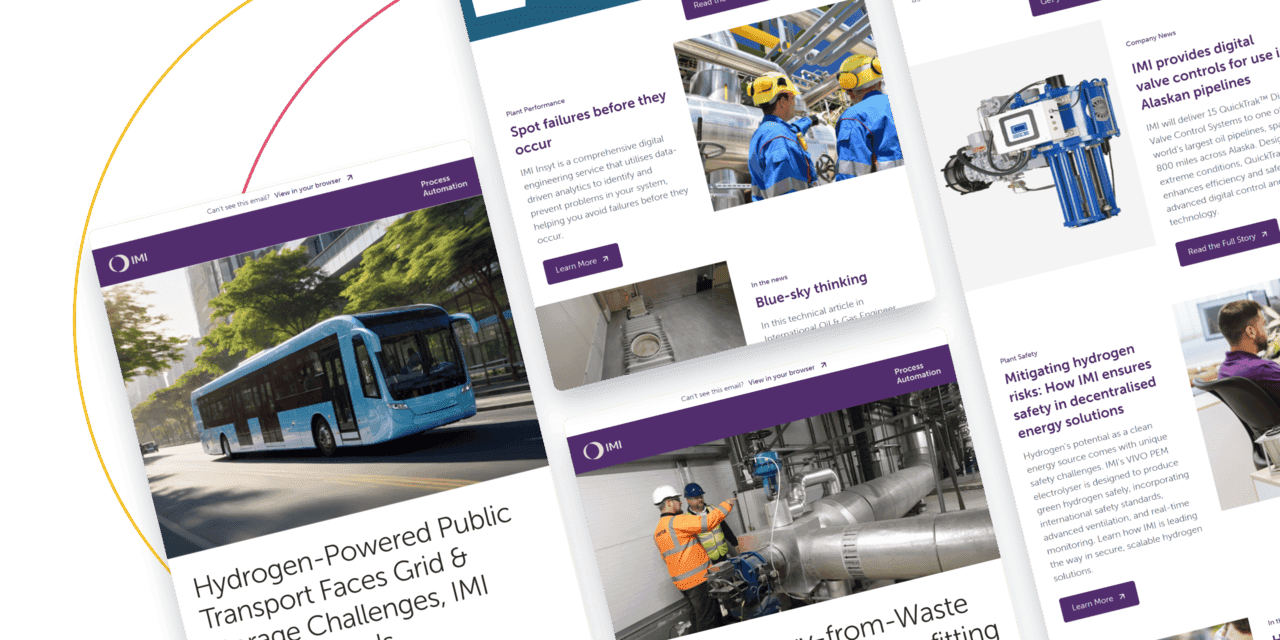
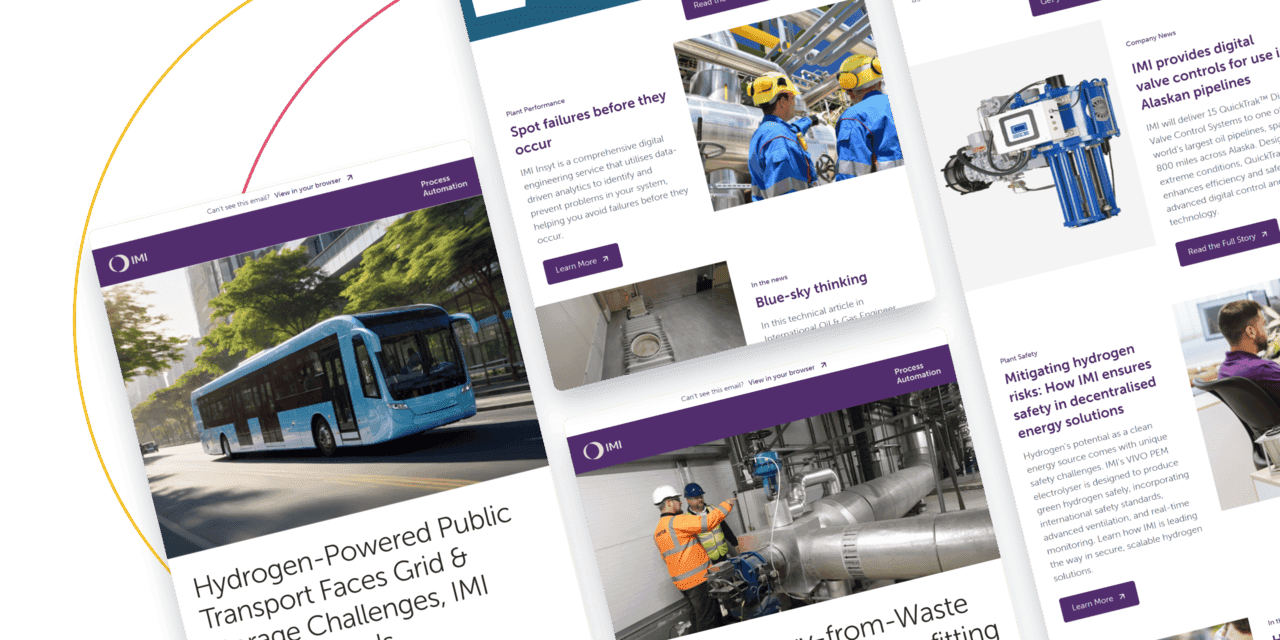
Keep in touch
Stay up to date on all the latest news and articles from IMI.
Engineering the future together
Looking for the perfect flow control solution? Our experts specialise in providing tailored solutions to meet your unique needs. Let us help you achieve optimal performance, efficiency and safety.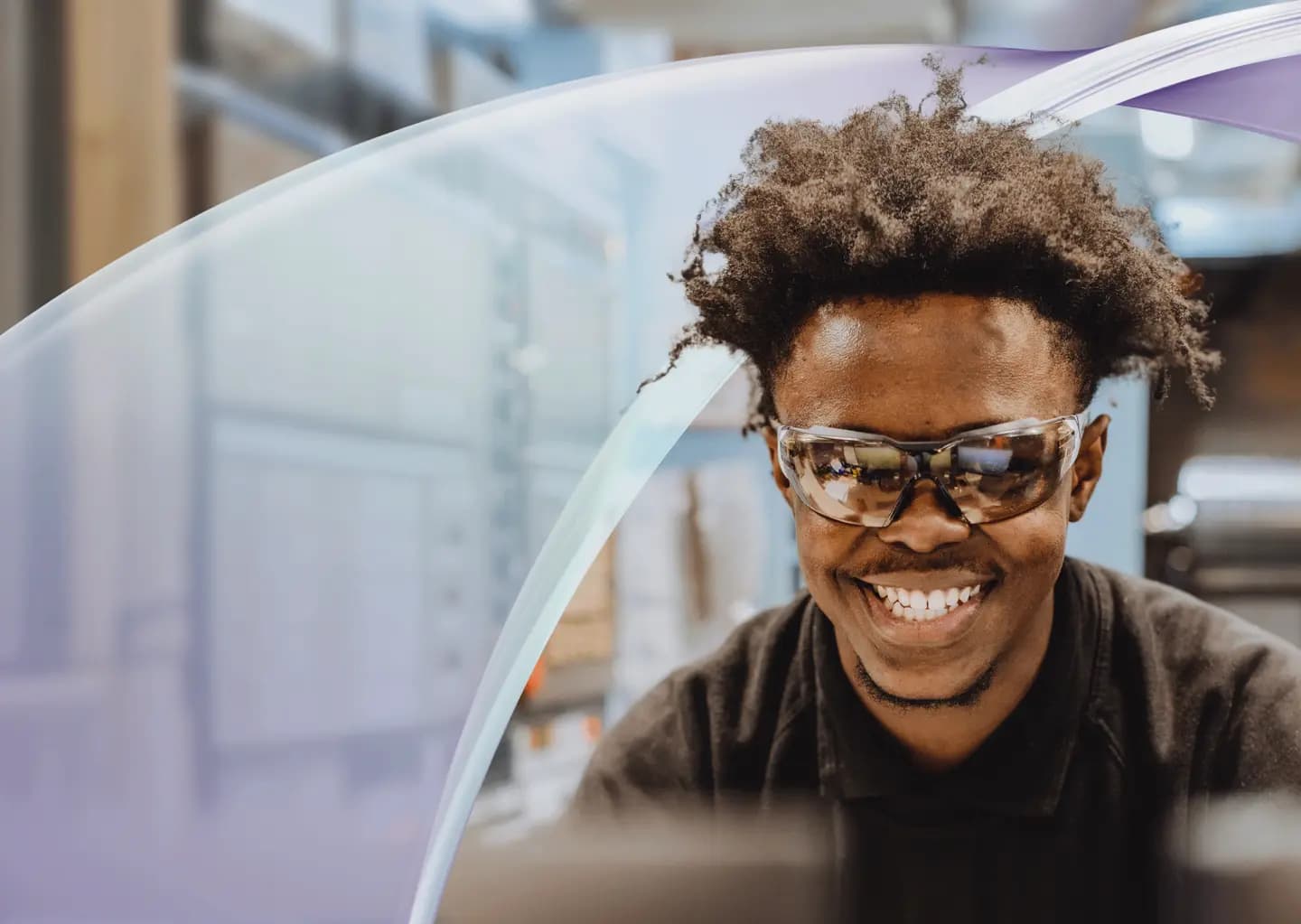