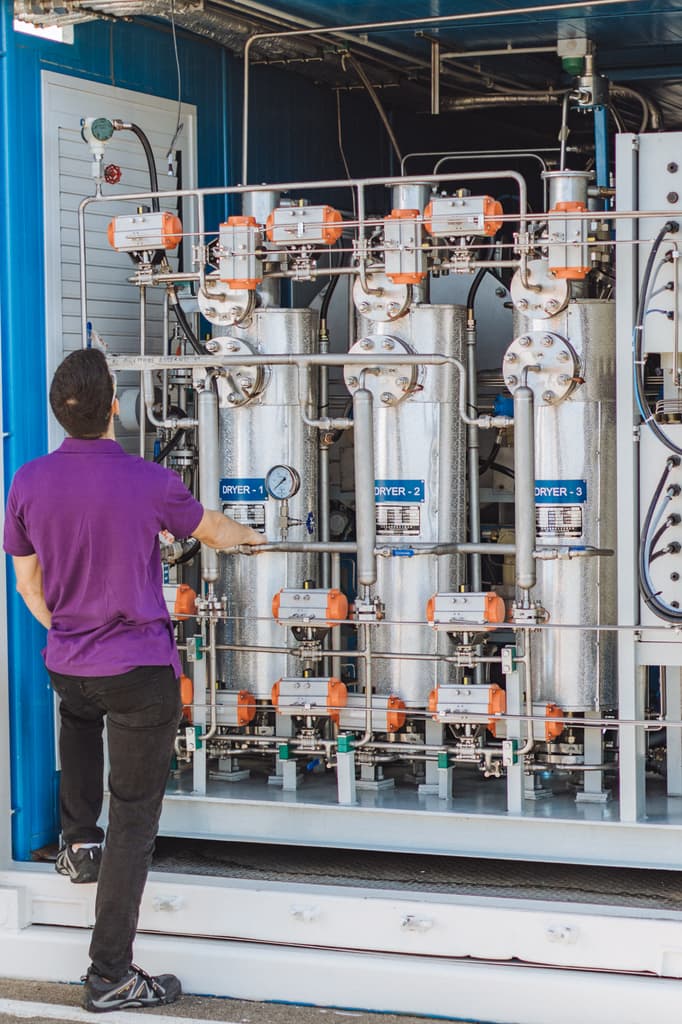
BLOG
Specifying a PEM Electrolyser: Five critical considerations for safer, smarter hydrogen production
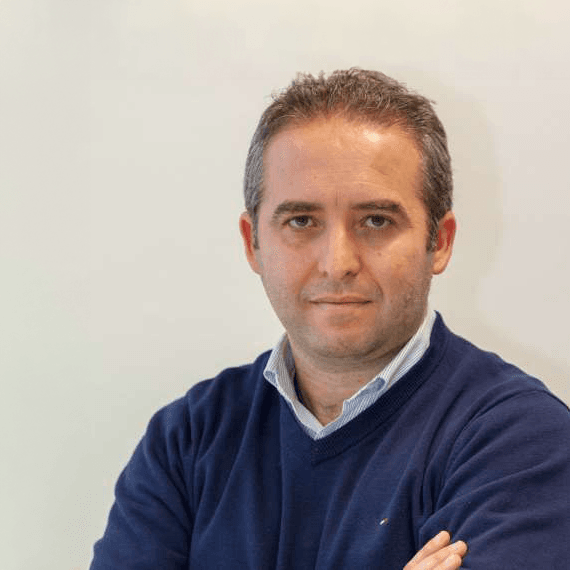
Written By Mauro Natalini
June 20, 2025
As the hydrogen economy gains momentum, Proton Exchange Membrane (PEM) electrolysers are emerging as a key technology in the transition to cleaner energy.
Selecting the right electrolyser, however, involves more than matching power requirements. Engineers and project teams must also consider safety, efficiency, site integration, and compliance. IMI designs and delivers highly engineered hydrogen solutions under its product brand, IMI VIVO. Our containerised and skid-mounted PEM electrolysers are used across industrial, mobility, and research applications, engineered to perform reliably and safely in demanding environments.
This article explores five key factors that should be evaluated when specifying a PEM electrolyser.
1. Understand the application and power class requirements
Hydrogen production requirements vary depending on the application. Whether the goal is decarbonising industrial processes, fuelling mobility infrastructure or supporting research, understanding how hydrogen will be used is essential. IMI VIVO’s PEM electrolysers are available in modular configurations from 1 MW to 5 MW, with scalable designs up to 20 MW. These containerised systems are particularly suited to:
Power-to-Gas (P2G) and Power-to-Process (P2P) installations
Hydrogen mobility infrastructure, where footprint and deployment speed are critical
Research facilities, where precise control and high-purity hydrogen are essential
All systems are customised to align with customer specifications and local regulatory standards.
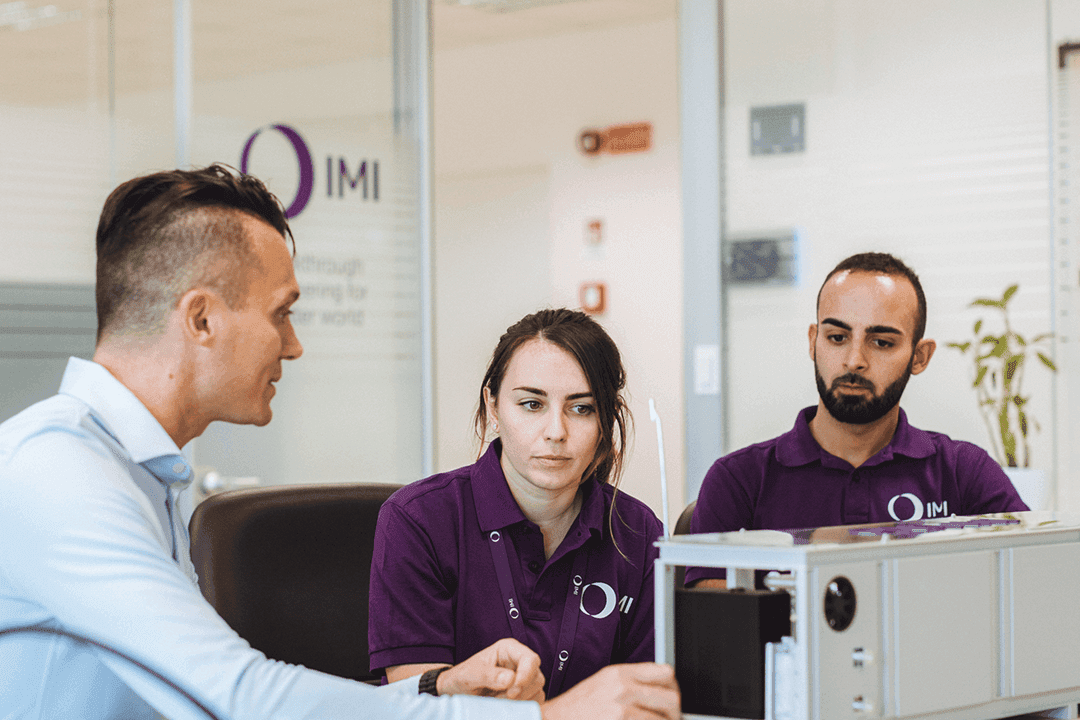
2. Prioritise energy efficiency to optimise total cost of ownership
PEM electrolysers are energy-intensive systems. Selecting an efficient unit can significantly reduce electricity usage, lower operating costs, and minimise environmental impact.
IMI VIVO’s PEM systems demonstrate strong performance across varying load conditions.
Incorporating optional heat recovery systems and reusing the oxygen stream where feasible can further improve overall system efficiency and sustainability.
3. Evaluate site constraints and deployment conditions
Space, noise sensitivity and installation timeframes often impact how and where hydrogen systems can be deployed. IMI VIVO’s “plug-and-play” containerised solutions address these challenges directly.
Each 5 MW unit includes:
Integrated PEM stacks and transformer-rectifier systems
Independent PLC/HMI control room
Chillers, dry coolers, and air systems
Separate water treatment system
A full system fits within a 12 x 45 x 13 ft footprint, designed for rapid onsite installation.
For installations in proximity to residential or commercial buildings, noise modelling tools are used during the design phase. These simulations help predict sound pressure levels and identify the need for mitigation such as acoustic barriers.
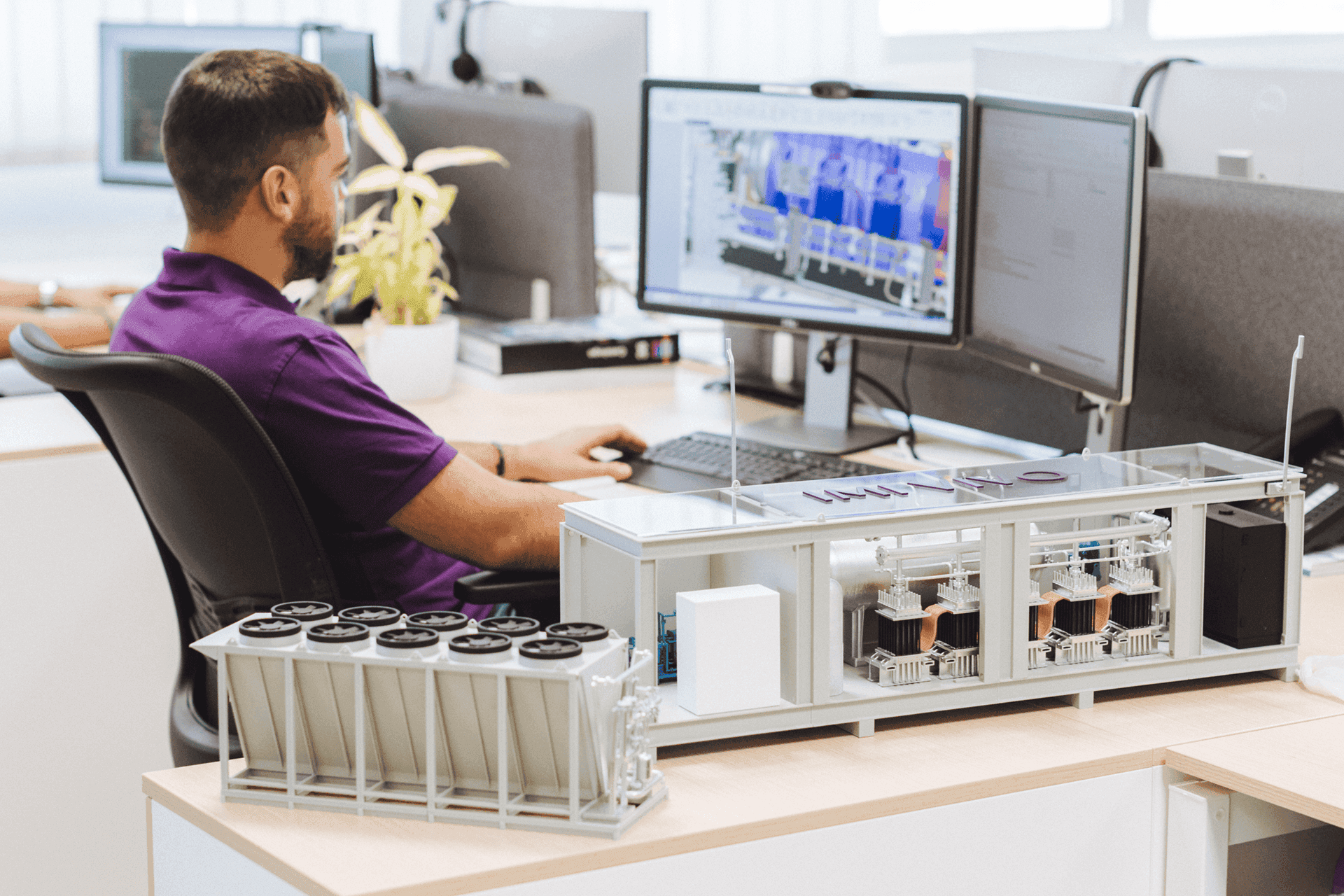
4. Prioritise safety from the start
Hydrogen production presents unique safety challenges. A robust safety strategy must be integrated into every aspect of electrolyser design and operation.
At IMI, safety is embedded through:
HAZOP (Hazard and Operability) studies to identify potential risks early in the design phase
SIL (Safety Integrity Level) classification of each Safety Instrumented Function (SIF), in accordance with IEC 61511
ATEX compliance, ensuring the safe operation of equipment in potentially explosive atmospheres
In addition, advanced simulations are used to verify the safety and resilience of the system:
Finite Element Analysis (FEA) simulates mechanical stresses in the event of an explosion, such as in an oxygen separator
Computational Fluid Dynamics (CFD) models hydrogen leakage scenarios and validates fan system performance in ventilating enclosed areas
These tools support the creation of designs that meet both regulatory and real-world safety demands.
If you want to dive deeper into this topic, take a look at Mitigating hydrogen risks: How IMI ensures safety in decentralised energy solutions.
5. Ensure compliance with local and international standards
Regulatory compliance is critical when deploying PEM electrolysers. Equipment must conform not only to international guidelines such as ISO 22734 (hydrogen generators using water electrolysis) but also to region-specific codes for pressure systems, electrical safety and environmental controls.
IMI VIVO electrolysers are built to meet a wide range of compliance requirements, including:
National fire safety and zoning regulations
Noise emission controls
Electrical grid integration standards
Environmental monitoring and reporting frameworks
Our engineering team works closely with customers to ensure systems meet both the technical and legislative standards of the installation location.
Case studies: Real-world PEM Electrolyser installations
IMI VIVO electrolysers are deployed across Europe in both industrial and research settings. Two recent examples include:
Translational Energy Research Centre (TERC), UK
100 Nm³/h electrolyser at 30 bar(g)
Supports the development of Sustainable Aviation Fuel (SAF) and the advancement of hydrogen and CO₂-based fuels to help decarbonise the aviation industry
Surplus hydrogen used for heating via converted boiler system
Powered in part by rooftop solar generation
If you want more information, take a look at How IMI is helping TERC pioneer sustainable fuels research
SARPOM Refinery, Italy
4 MW PEM electrolyser used to pilot green hydrogen integration into refinery processes
Expected to generate 167 tonnes of hydrogen annually
Supported by a 7 MW solar farm
Incorporates a custom electrical configuration with dual IGBT rectifiers and DC bus infrastructure
You can learn more about this installation at IMI 4MW PEM Electrolyser boosts green hydrogen production at API Sarpom refinery
Conclusion: Choosing the right electrolyser partner
Specifying a PEM electrolyser is a strategic decision involving multiple technical, commercial and regulatory factors. The system must not only meet your current needs, but also support future scaling, integration and safety standards.
At IMI, our engineers work directly with customers to design solutions that are tailored, compliant and future-ready. With decades of experience in demanding hydrogen and energy applications, IMI VIVO electrolysers are built to enable safer, more efficient and more sustainable hydrogen production.
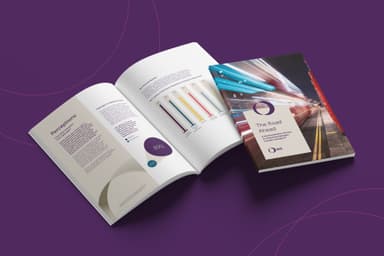
The Road Ahead
Is decentralisation the key to unlocking hydrogen in public transport?
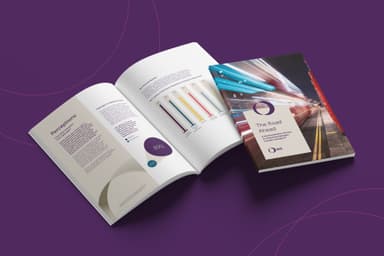
The Road Ahead
Is decentralisation the key to unlocking hydrogen in public transport?
Keep in touch
Stay up to date on all the latest news and articles from IMI.
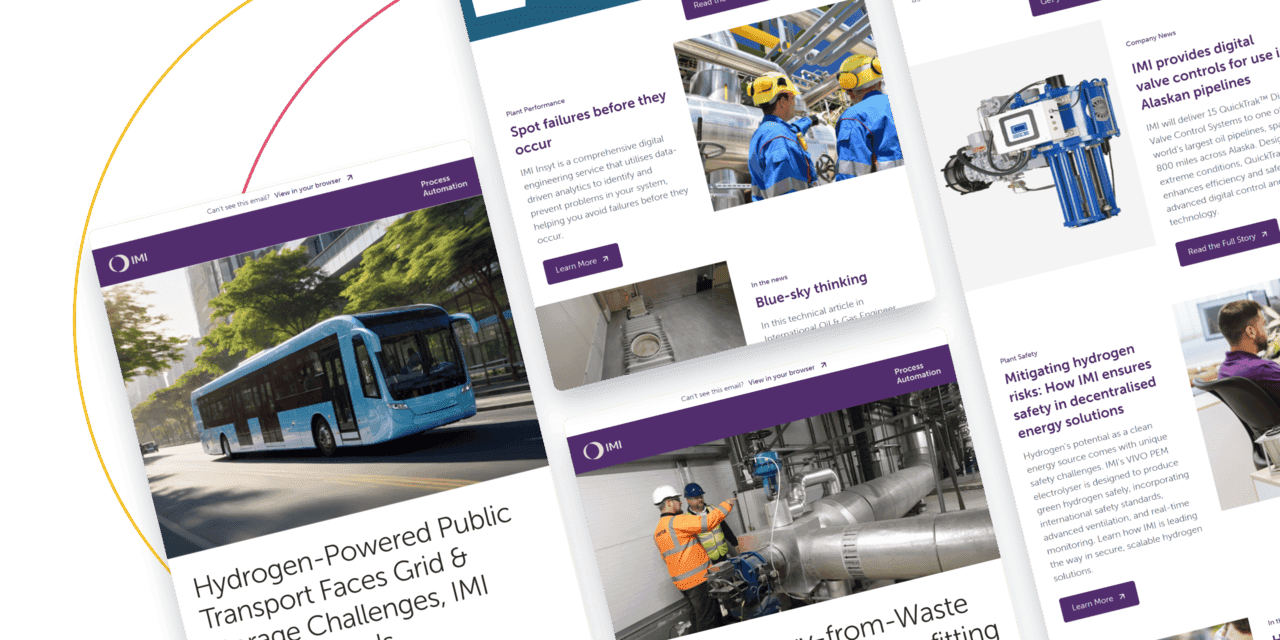
Keep in touch
Stay up to date on all the latest news and articles from IMI.
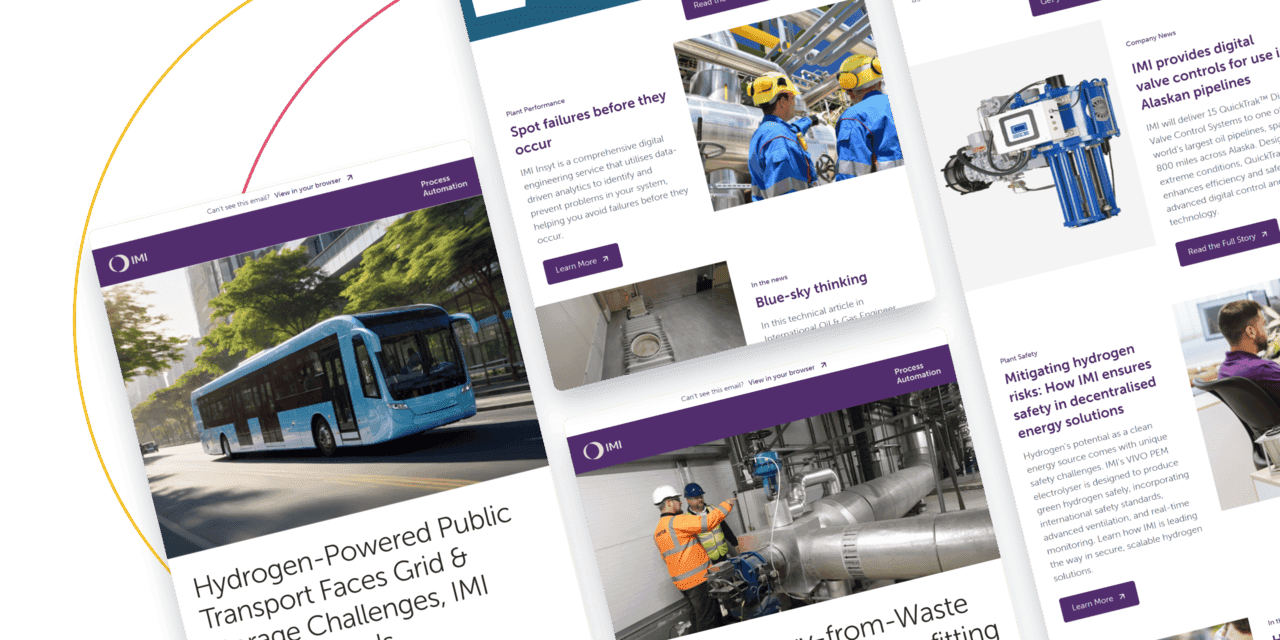
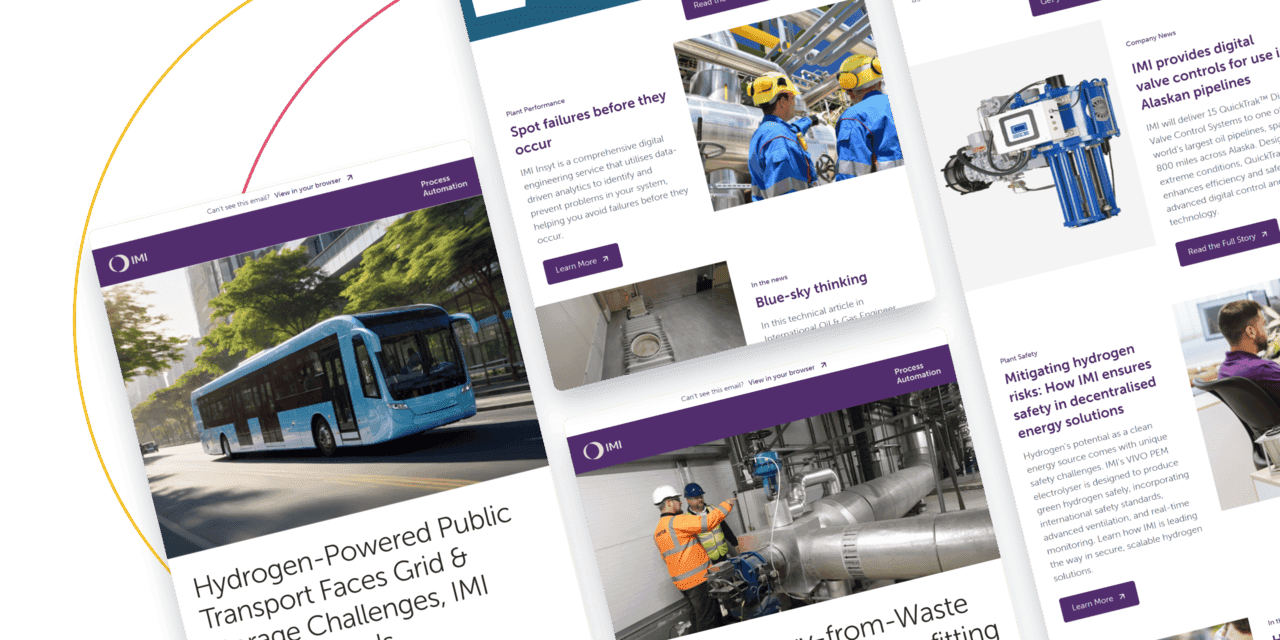
Keep in touch
Stay up to date on all the latest news and articles from IMI.
Engineering the future together
Looking for the perfect flow control solution? Our experts specialise in providing tailored solutions to meet your unique needs. Let us help you achieve optimal performance, efficiency and safety.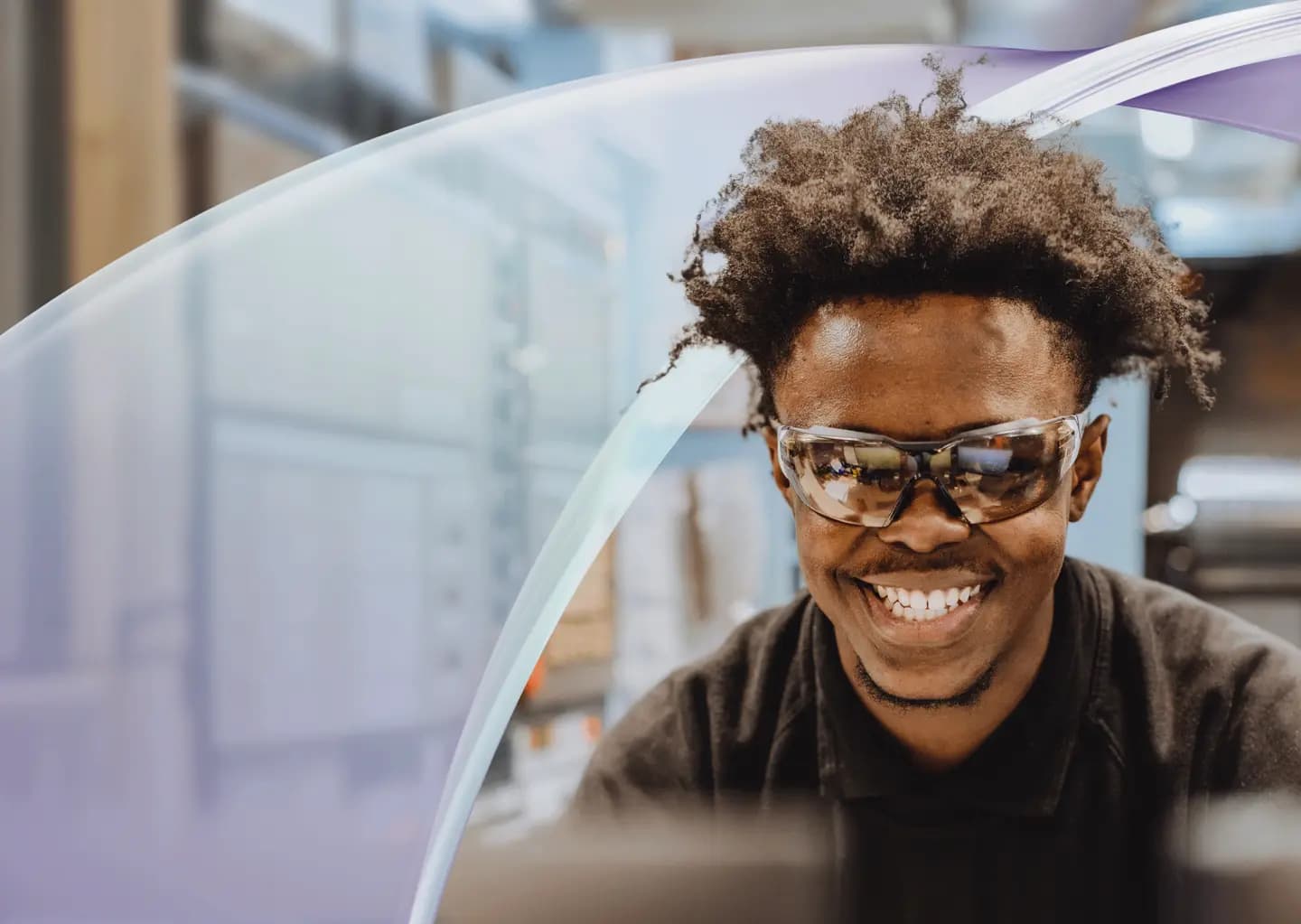