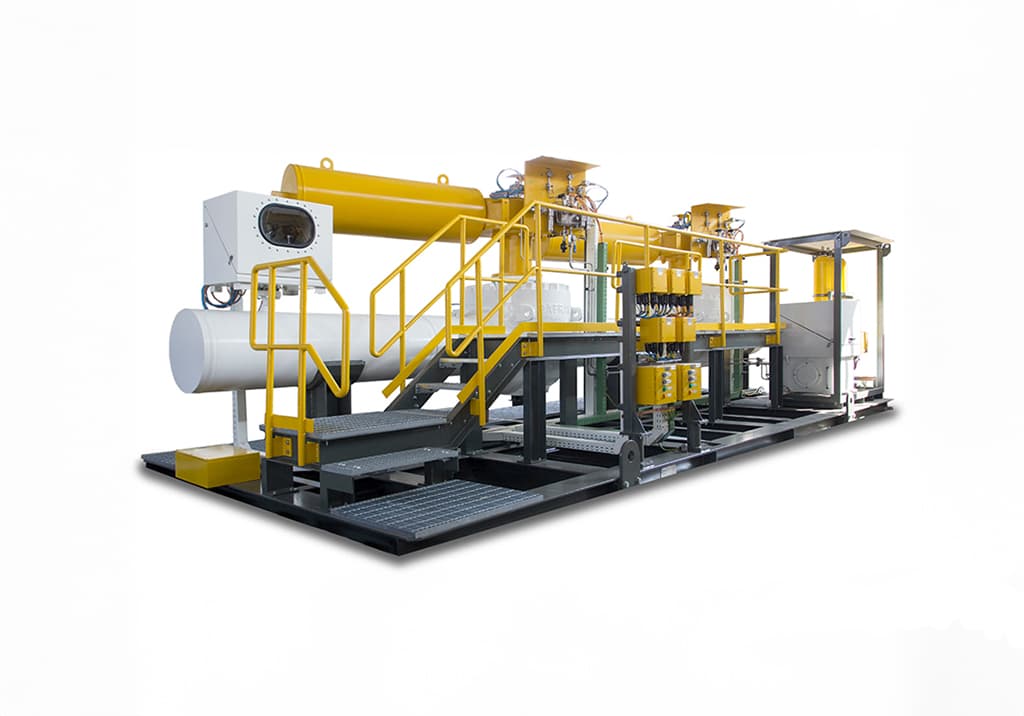
BLOG
HIPPS and Functional Safety: Smarter protection in a changing world
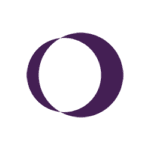
Written By IMI Publications
July 25, 2025
In today’s process industries, functional safety isn’t a one-time decision - it’s a continuous commitment. As risks evolve and operational demands grow, manufacturers need smarter, faster, and more robust ways to protect people, assets, and the environment.
That’s where High-Integrity Pressure Protection Systems (HIPPS) come in.
What is HIPPS?
A HIPPS is an independent safety instrumented system (SIS) designed to detect abnormal process conditions—such as high pressure—and rapidly isolate the source to prevent a hazardous release. It acts as the final barrier between safe operation and a potential incident.
Unlike traditional relief valves and flare systems, HIPPS:
Activates quickly and accurately to perform the required safety function
Prevents unnecessary flaring and emissions
Reduces wear on downstream equipment
Helps meet strict global safety and environmental regulations
HIPPS systems are built in line with international safety standards such as IEC 61508 and IEC 61511, and are designed to meet required Safety Integrity Levels (SIL)—from SIL 1 to SIL 4.
Why functional safety matters now more than ever
From decarbonisation goals to digitalisation and resource constraints, today's energy landscape is rapidly changing. At the same time, industry safety expectations are rising.
To navigate this, operators are turning to more sophisticated protection layers—including advanced HIPPS solutions - to mitigate risk, improve sustainability, and support plant reliability.
Understanding the risk
Risk is the product of a potential hazard and the likelihood of it occurring. HIPPS directly addresses both:
It prevents escalation of hazardous events
It reduces risk to tolerable levels by stopping the release of high-pressure fluids before failure occurs
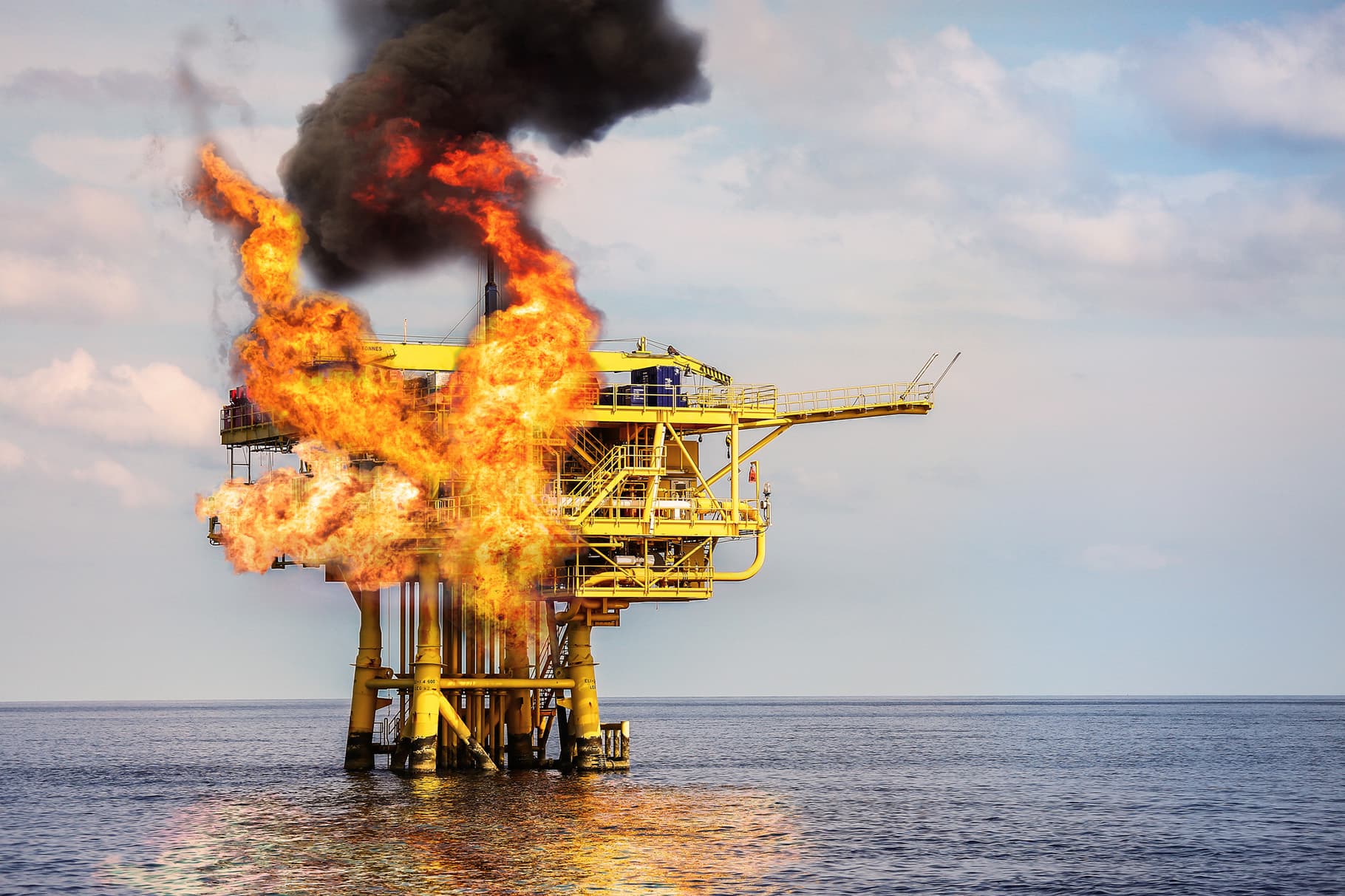
HIPPS systems keep your facility safe
How HIPPS works
HIPPS typically consists of three key subsystems:
1. Initiators
These measure process parameters (e.g. pressure, temperature, or level) and trigger the logic solver if limits are exceeded. IMI’s approach includes:
Sensor voting logic (e.g. 2oo3)
Transmitters with built-in diagnostics
Interlocking manifolds for online calibration
2. Logic Solver
This is the control unit of the system. IMI offers both programmable and solid-state options, depending on SIL requirements. Features include:
Redundant architecture
Formal verification tools to confirm safe logic behaviour
High diagnostic coverage
3. Final Elements
These are elements that protect downstream equipment from the hazardous event. IMI supplies:
Ball, gate, butterfly, and axial valves tailored to process conditions
Fast stroking actuators with low pressure drop
Single or multiple valve configurations (SIL 2–4)
Measuring safety performance
HIPPS are not only designed for safety and reliability—they’re tested for it. Safety performance is evaluated using key metrics such as:
Probability of Failure on Demand (PFD)
Diagnostic Coverage (DC)
System uptime
IMI applies formal analysis methods and works with third-party certification bodies to ensure compliance at every stage.
Flexible solutions, built to standard
From fully mechanical systems to complex electronic architectures, IMI designs each HIPPS to the specific needs of the site, process, and safety target.
We provide:
—ideal for remote or power-limited environments, offering SIL-rated protection with no electrical input required
—custom-engineered systems designed for high-end functional safety and diagnostic capability
All IMI systems are compliant with IEC standards and delivered with full documentation, FATs/IFATs, and SIL certificates.
The IMI difference
Our customers choose IMI because we bring more than just products - we bring end-to-end capability:
Expertise in safety system design and integration
Component selection from our global product portfolio
Factory-assembled, third-party certified systems
Ongoing support throughout the system lifecycle
IMI holds a Functional Safety Management (FSM) certificate issued by a Notified Body. All personnel involved in sales, design, testing, and commissioning are certified Functional Safety Engineers, also accredited by a Notified Body.
Whether you're safeguarding a remote wellhead, an FPSO, an FLNG unit, a storage tank, a regasification facility, or a downstream separator, our HIPPS solutions are engineered to elevate both your safety performance and your peace of mind.
Let’s talk safety
Ready to improve plant protection, reduce emissions, and achieve functional safety targets?
Contact us today to learn how HIPPS can support your goals - whether you need a standalone system, an upgrade path, or a full site risk assessment.
Keep in touch
Stay up to date on all the latest news and articles from IMI.
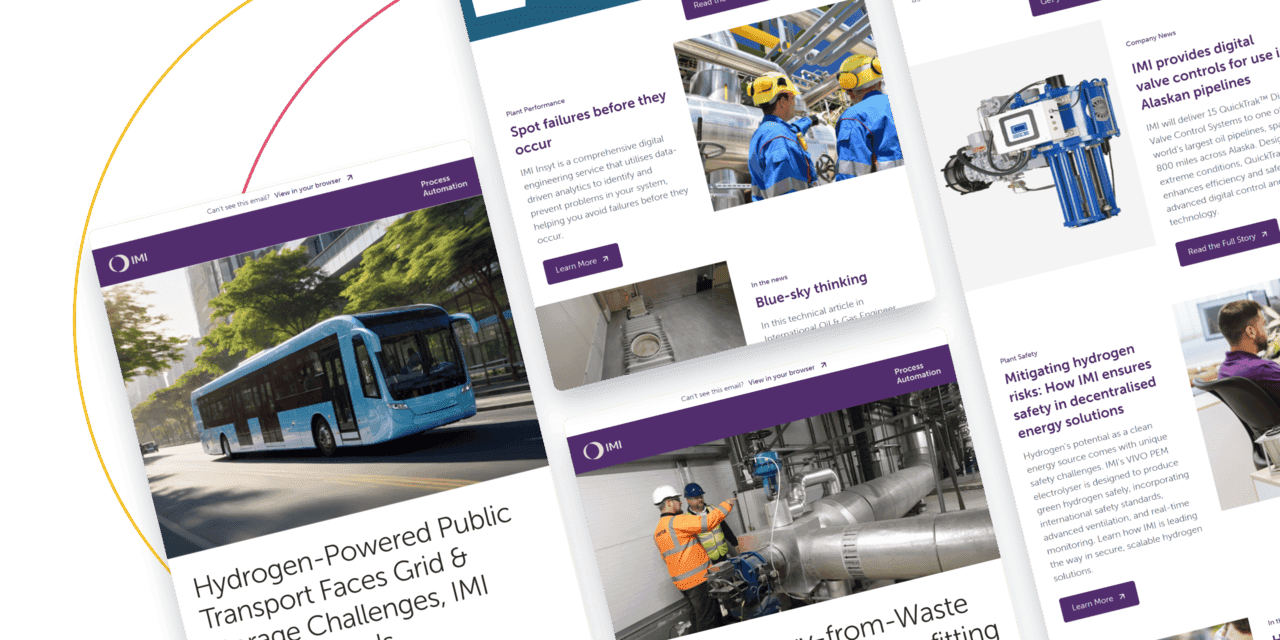
Keep in touch
Stay up to date on all the latest news and articles from IMI.
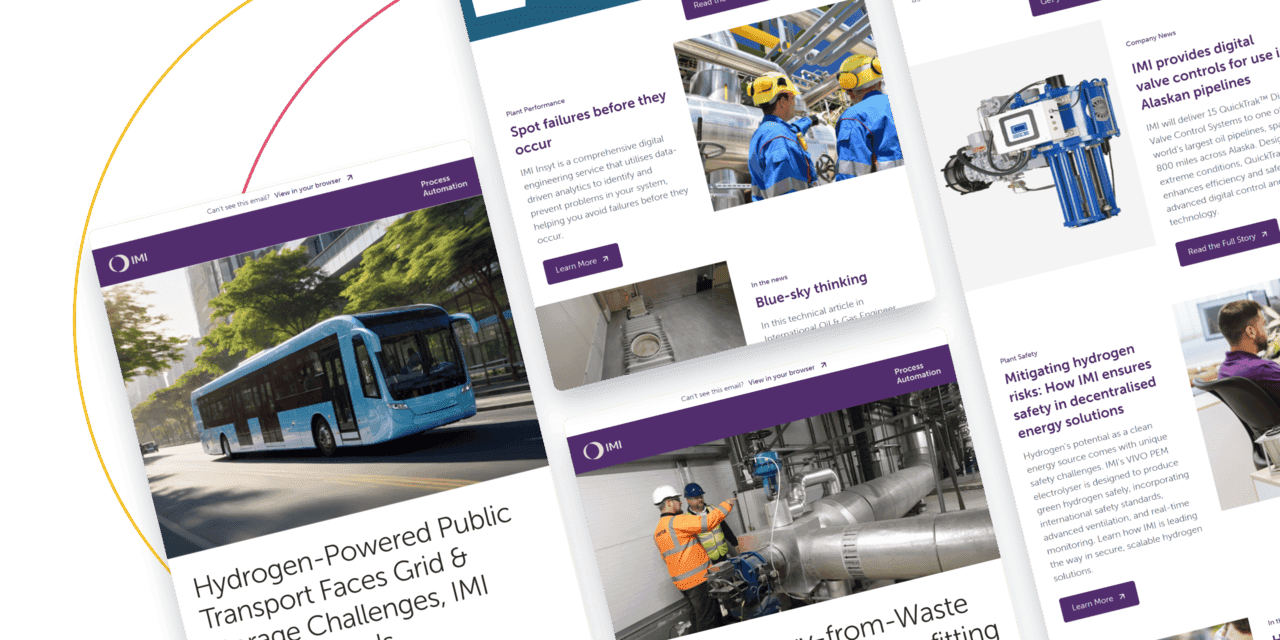
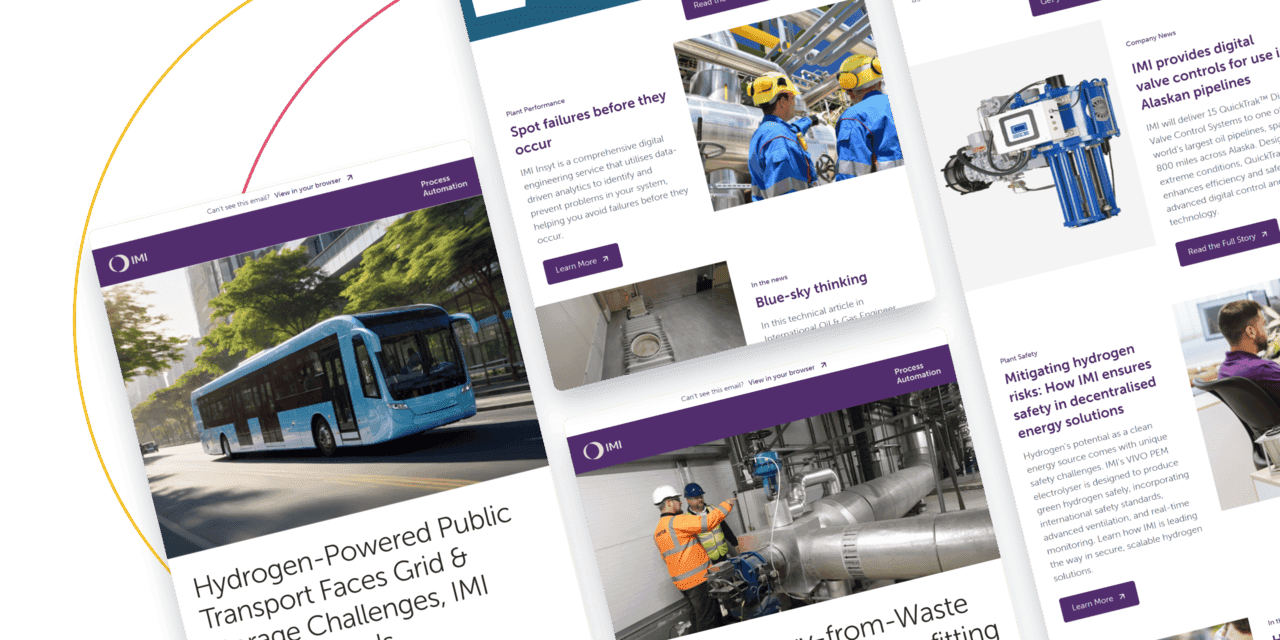
Keep in touch
Stay up to date on all the latest news and articles from IMI.
Engineering the future together
Looking for the perfect flow control solution? Our experts specialise in providing tailored solutions to meet your unique needs. Let us help you achieve optimal performance, efficiency and safety.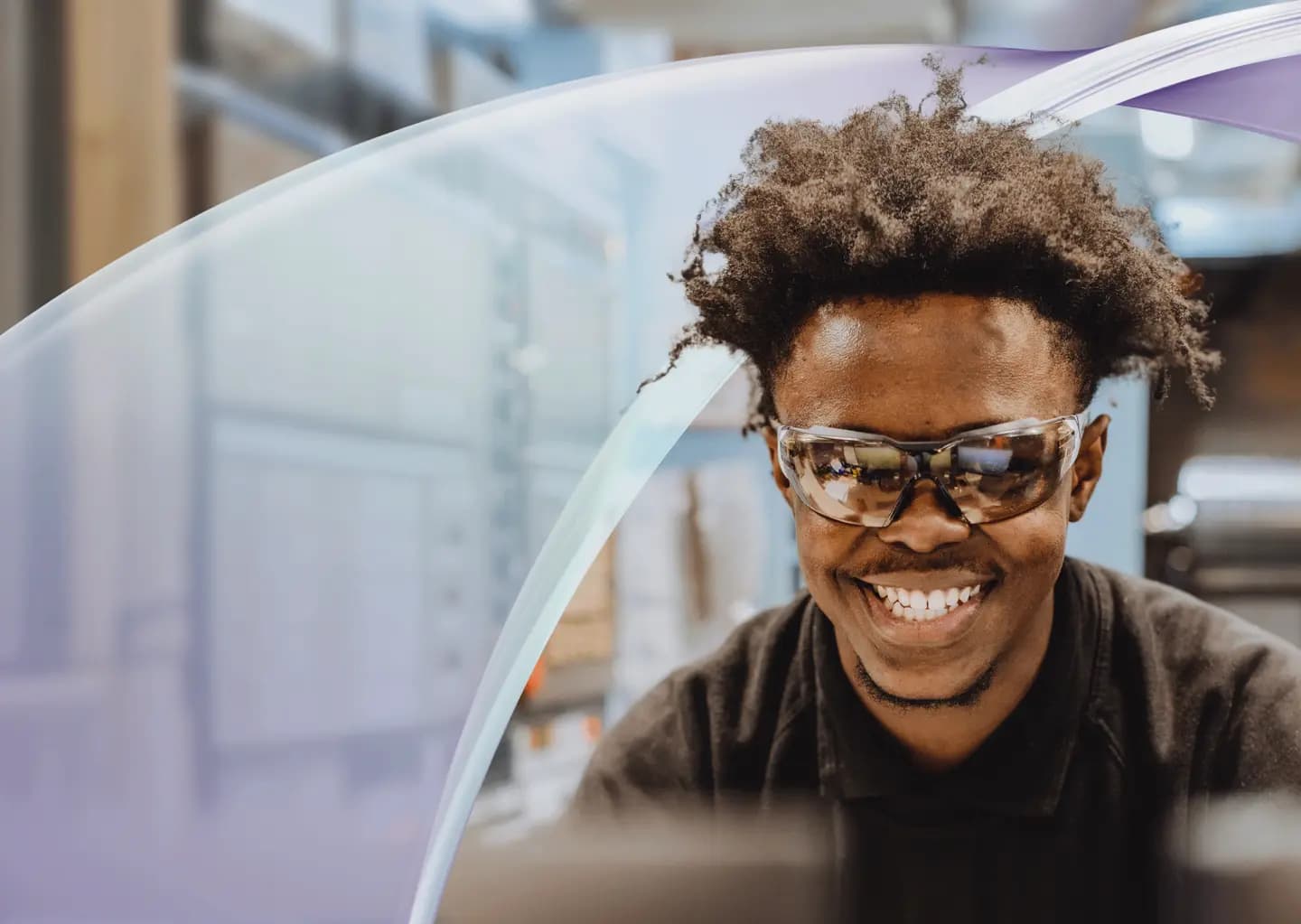